Sterile Filtration Strategies

It is critical that drug products are free from bacteria and other microorganisms to ensure patient safety. For pharmaceutical products that cannot be terminally sterilized, expertise in filtration solutions such as aseptic filtration can help meet these challenges.
Ensuring performance of sterile filters with integrity testing
Sterile filtration is commonly employed for microbial removal and plays a pivotal role in assuring final product sterility. Where sterility will be claimed, regulatory agencies worldwide require that the sterilizing-grade filter(s) be integrity tested to ensure filter performance is verified prior to and after filter use. Therefore, successful filter integrity tests are a critical link between filter validation and current processing. Designing a robust integrity test operation can help to ensure reliable filter integrity tests.
Related Resources
- Best Practices for Critical Sterile Filter Operation: A Case Study
A number of regulatory guidelines recommend preuse integrity testing of critical sterilizing liquid filters for aseptic processing.
Assuring sterile drug product with a Small Volume Parenteral (SVP) process
Filtration of liquids through sterilizing grade filters is a common method for removing microorganisms from SVPs, especially those that are heat-sensitive. Final filtration with a 0.22 µm filter is the last unit operation in the process and is a critical step for successful manufacturing of a parenteral drug formulation.
Regulatory requirements and industry best practice help assure this critical process step is effective. Additionally, a comprehensive validation strategy provides the scientific evidence to confirm that process conditions and filters are robust and to defend these decisions to regulatory authorities. Use of sterilizing grade filters for removal of microorganisms should follow critical guidelines for incorporating this step late in the manufacturing process to ensure sterility.
Minimizing risk of contamination through Quality by Design (QbD)
The selection of an effective and efficient sterilizing grade filter is essential to provide sterility assurance. Understanding filtration systems and components can be a challenge, given the array of different options. Design and manufacture of filtration system components should apply QBD principles to provide high assurance of sterility for aseptic processes.
Defining validation and qualification strategies
Sterilizing filtration must be qualified during early clinical phases to demonstrate the ability to provide a sterile product without adversely affecting its properties. The filter, as critical equipment used for manufacturing a sterile investigational drug, should not contaminate or otherwise react with, add to, or be absorbed by the drug. Understanding the key elements of sterile filtration, validation, and regulatory guidance for developmental phase drug products is critical to ensuring that the process is properly defined and validated.
To assess the performance of a filter and thereby ensure the quality of the product, several aspects need to be examined including bacterial retention, chemical compatibility, extractables, and adsorption. A defined validation strategy helps ensure that processing conditions are optimized, and filters are tested to confirm their performance.
Related Webinars
Filtration of liquids through sterilizing grade filters is a common method for removing microorganisms from small volume parenterals that are heat-sensitive.
In aseptic processing of pharmaceutical products, it is critical that drug products are free from bacteria and other microorganisms to ensure patient safety.
Workflow


Liquid formulation strategies
Sterile liquid applications are often injected into the body, making it critical to minimize risk by choosing the right process to purify the API, identifying suitable excipients, defining appropriate process validation, and selecting the right filters.
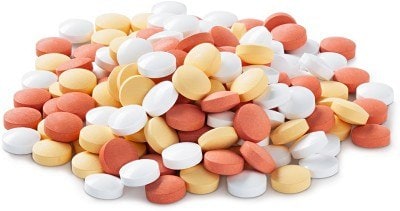
Solid formulation strategies
Drug products must be free from bacteria and other microorganisms to ensure patient safety, requiring expert use of aseptic filtration for pharmaceutical products that cannot be terminally sterilized.

Final fill strategies
The final fill process is a critical aspect of drug manufacturing, demanding careful risk mitigation in order to ensure that safe therapeutic drug products are provided to patients.
To continue reading please sign in or create an account.
Don't Have An Account?