3D-Printable Inks for Energy and Environmental Applications
Swetha Chandrasekaran<sup>1</sup>, Annemarie Meike<sup>2</sup>, Marcus A, Worsley<sup>1</sup>
1Staff Scientist, Materials Science Division, Lawrence Livermore National Laboratory, 2Business Development Executive, Innovations and Partnership Office, Lawrence Livermore National Laboratory
Introduction
Partnering additive manufacturing (3D printing) with functional nanomaterial-based inks has the potential to push the properties and performance of advanced materials beyond previous capabilities. This is particularly true in energy and environmental applications. Graphene, 2D materials, and ceramic-based inks, when coupled with 3D printing technologies like Direct Ink Writing (DIW), also called “robocasting,” have shown promise to greatly enhance the performance of batteries, supercapacitors, reactors, and separator devices. Robocasting enables the printing of large-scale electrodes for energy applications with micron resolution by using high concentration viscous inks.
DIW inks of various compositions have been crafted that enable 3D printed products for (1) energy storage, (2) energy conversion, sensing, and catalysis, and (3) filtration and separation under extreme conditions.
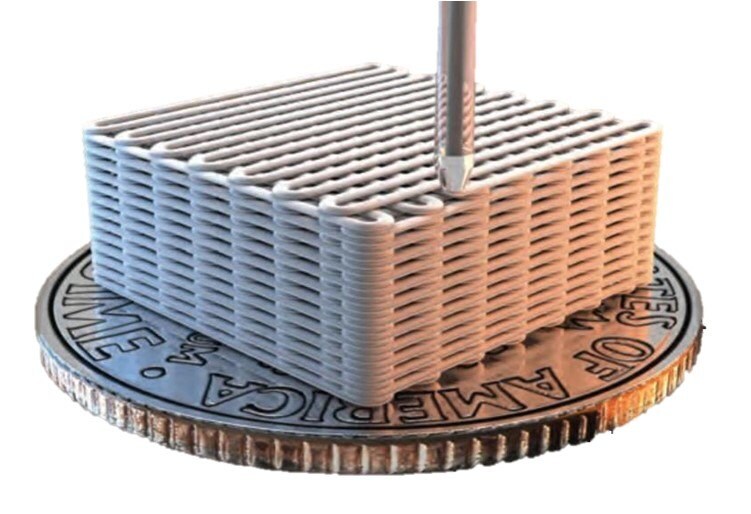
Figure 1.llustration of 3D-printed materials generated using product number 916579.
Inks for Energy Storage Applications
Next generation energy storage technologies will require graphene and carbon aerogels that enable 3D printed products.
Efficient energy storage technology continues to be a key challenge for a wide range of industries. While conventional battery technologies represent most of the current energy-storage market, their inherent limitations in charge/discharge rate, cycle life, and reliability have spurred interest in the design and engineering of advanced materials and architectures. 3D-printable electrochemically active materials allow optimized electrode and device architectures. For example, 3D-printable graphene-based and carbon-based inks could enable fast charge/discharge rates, increase cycle-life, and improve gravimetric capacitance for next generation energy products (e.g., electrochemical energy storage devices) through the implementation of aerogel electrodes with controllable, percolated, vascular structures. Percolated vascular electrode architecture could enable fast charge transport kinetics, while built-in porosities within the electrode could compensate charge-injection-induced large-volume changes. Both strategies are hard to achieve using conventional manufacturing methods. Carbon aerogels and 3D-printed graphene spur innovation in alternative storage devices—e.g., supercapacitors—while also allowing access to new device architectures for conventional lithium-ion batteries.
3D printed graphene electrodes address the trade-offs between the gravimetric (weight), areal (surface area), and volumetric (total volume) capacitance of supercapacitor electrodes that were previously thought to be unavoidable. In previous uses of pure graphene aerogel, volumetric capacitance suffered due to the inherent low density of aerogels. This issue is exacerbated with 3D-printed graphene aerogel electrodes because volumetric capacitance is reduced even further due to the periodic large pores between the printed filaments.
LLNL, in collaboration with the Li group at University of California – Santa Cruz, developed a 3D-printed graphene aerogel using product number 916579 with MnO2 electrodes, that has achieved high volumetric capacitances, hundreds of times higher than pure graphene aerogel electrodes.1 The key innovation in this work is the use of 3D printing to fabricate a rationally designed structure providing a carbon scaffold to support the pseudocapacitive material. Moreover, the 3D-printed electrode has an open structure that ensures excellent coverage of functional groups on carbon surface and facilitates the ion accessibility of these surface functional groups even at high current densities and large mass loading/electrode thickness.2
Energy Conversion and Reactors
Graphene-analog or 2D materials (e.g., transition metal dichalcogenides) that offer chemical inertness, catalytic activity, and low density. After a noticeable decline in the previous decade, hydrogen fuel-cell technologies are once again attracting significant interest both from the perspective of basic research and in specialized industrial applications. However, the cost and difficulty of producing sufficient quality hydrogen feedstocks remains a key challenge to fully implementing these technologies. Printable energy conversion devices utilizing 3D printable inks will enable proof-of-concept lab-scale studies and industrial R&D validation of energy storage devices. Such materials will enable 3D printing of energy-conversion devices (e.g., hydrogen evolution) and catalytic reactors (e.g., fuel upgrading).
Inks for Extreme Environmental Applications
a) Filtration and Separations: Ceramic feedstock inks that survive harsh or extreme conditions, including micro-/nano-porous ceramic materials—such as yttria-stabilized zirconia (Product Number 918571). Resistance to harsh environments is important in many applications. One example is lithium-ion batteries, where capital investments limit innovation of device architectures. In these cases, product number 918571 will allow for the creation of efficiency-performance-enhancing components that can be easily incorporated into existing device structures. These feedstocks are both chemically and mechanically robust at extreme temperatures and high pH, and thus should enable significant advances in 3D printing energy storage/conversion, separations, and sensor devices. A major advantage of 3D printing lies in the flexibility to create components that can be designed for easy incorporation into existing devices.
Porous ceramics are ideal for applications in filtration, catalysis and thermal insulation because of characteristics, such as high surface area and tunable porosity (including nano-porosity) and microstructure based on processing conditions and raw materials.3–5 Our developed porous YSZ ceramic paste to support CO2 separation using a dual-phase (liquid/solid) membrane. The developed dual phase membranes operate at flue gas temperatures (300-700 °C) and can easily be used to retrofit in current power plant designs, utilizing existing boiler or heat recovery steam generator infrastructure in conjunction with a low pressure steam sweep. This, in turn, could allow for a significant reduction in carbon emissions without the need to replace the current fleet of coal and natural gas power plants worldwide.6
b) Ultra-high-temperature ceramics, for applications requiring lightweight, super-hard materials, such as boron carbide ceramics. Ultra-high-temperature ceramics (UHTCs), used for heat exchangers and other components subjected to extreme temperatures, are extremely hard yet difficult to machine in complex shapes required. Additive manufacturing with our 3D-printable inks (Product Number 921912) overcomes this challenge. A thixotropic ink with a high-volume fraction of aqueous ceramic suspension is extruded through a micro nozzle to pattern complex and graded 3D structures.
Boron carbide (B4C) (Product Number 921912), a low density, low chemical reactivity, high melting point, ultra-high temperature ceramic, is often used for extreme environment applications. Common uses include high wear components, control rods for fast-breeder nuclear reactors, and light-weight armor applications.7 The gel casting technique is the typical manufacturing process employed to make complex shapes. However, this method presents obstacles while casting high volume suspensions and often requires a curing agent or harsh cross-linking polymers.8
DIW fabrication offers an excellent means of manufacturing components embedded with functionally graded materials, using a technique that is fully capable of production scale quantities. The application of DIW to gradient body armor is a good example. Using DIW, one can deposit layers of B4C-Al cermets with varying amounts of B4C so the armor plate can have the designed hardness and fracture strength gradient through the thickness.9
References
続きを確認するには、ログインするか、新規登録が必要です。
アカウントをお持ちではありませんか?