Liquid Formulation Strategies

Many drugs are administered in liquid form. Whether injected, infused, consumed orally or applied topically, these therapeutics present unique challenges to formulators. For successful administration via these routes, the active pharmaceutical ingredient (API) must have sufficient solubility and stability. Additional criteria can apply depending on the administration route, such as a defined pH, tonicity or viscosity range to ensure applicability and/or tolerability, optimized taste to improve patient compliance, low bioburden and endotoxin levels or, i.e. for injectables, tested sterility of the final drug product to minimize risk for the patient.
To determine which solution is best suited for a specific API and its formulation requirements, it is important to understand how, and which excipients can help overcome these challenges and key considerations for selecting the best approach.
Related Technical Articles
- Media variability is a major concern for the biopharmaceutical industry. A wideranging program to evaluate and understand the variability is critical to produce consistent quality cell culture products. Raw Material Characterization (RMC) was launched to fulfill the unmet need in the industry.
- See All (1)
Explore our comprehensive portfolio of excipients for liquid formulation and active pharmaceutical ingredients for addressing each of these challenges and reducing the risk in development and manufacturing.

Improving API Solubility
Solubility is a prerequisite for ensuring bioavailability and the desired therapeutic effect. With an estimated 70–90% of drugs currently in development being poorly water soluble, finding adequate solutions to overcome this challenge is increasingly important and urgent.
- The solubility and stability of small molecules can be addressed with a variety of techniques including formulation and API processing.
- API processing is performed in early phases of drug development and leverages strategies such as salt and cocrystal formation to improve API properties, including enhanced solubility.
- Among the most versatile excipients used in liquid formulations are cyclodextrins and surfactants.
- Surfactants stabilize emulsions or suspensions and can also enhance solubility. New approaches are available such as self-emulsifying drug delivery systems.
- Cyclodextrins can be used to improveboth API solubility and stability.
- In addition to its application as a counter ion in salts, meglumine can be also used as functional excipient to enhance API solubility, improve API stability, and adjust pH value.

Minimizing Risk in High-Risk Applications
Parenteral preparations are high-risk formulations. Because of their route of administration, the potential of contaminations to cause harm is higher compared to other routes of administration such as oral or topical delivery.
- Strict regulations apply and the final drug manufacturer must take precautionary measures to minimize risk throughout the production, select appropriate raw materials, and reduce bioburden levels.
- Excipients can be used to optimize processes, protect, support, and improve stability and bioavailability, modulate release of the API, and enhance effectiveness of the drug. For injectable applications, considerations how to minimize excipient risks are very important.

Ensuring Safety and Tolerability of Ophthalmics
Formulating ophthalmic drugs presents unique challenges. Multiple factors must be appropriately balanced including tonicity, pH, and viscosity are necessary to ensure safety, tolerability, and efficacy of the medication. In parallel, low bioburden must be ensured throughout the shelf-life and usage period.
- Excipients play an important role in ophthalmic dosage forms, having a direct impact on critical process parameters and critical quality attributes. Polymers are particularly well-suited for ophthalmic dosage forms, offering several important benefits.
- Polyvinyl alcohol (PVA) offers many advantages for ophthalmic formulations. This excipient can be used for different applications such as retention in the eye cavity and solubility, and is compatible with a range of other excipients.

Increasing Shelf Life and Limiting Microbial Contamination
Pharmaceutical formulations, especially liquid and semi-solid formulations, are susceptible to unwanted microbial contamination. If preventive measures are not taken, this will severely impact product shelf life and patent safety. Preservatives may be used to protect formulations from contamination as well as ensure the necessary shelf life.
- Selecting the best preservative for a specific formulation requires consideration of many factors.
- Benzalkonium chloride is frequently used as a preservative due to its wide anti-microbial and broad pH range activity. It is used in ophthalmic formulations as well as transmucosal, otic, topical, and inhalation indications.
- Benzyl alcohol is a preservative used in injections, topical, oral and otic applications. It is also used as a stabilizer and because of its anesthetic properties it can be used to reduce pain on injection.
- Methylparaben is commonly used as a preservative in combination with propyl-paraben or propyl 4-hydroxybenzoate. Paraben salts, such as methylparaben sodium salt, have better water solubility and as such, may be preferred in formulations.
- Benzoic acid and sodium benzoates are used for low-risk pharmaceutical and food applications. Sodium benzoate has much higher water solubility and as a result, is used in a large number of products including a high percentage of oral liquid preparations.

Improving Process Efficiency
Manufacturing processes must be designed to bring new therapies to market faster and more cost effectively. A key to workflow efficiency is avoiding process interruptions, quality deviations and operator safety risks.
- Caking and clumping of chemicals, dust formation, and laborious weighing processes reduce efficiency. Solutions such as granulated raw materials, which are free-flowing and have reduced caking behavior, can improve processability, accelerate production, and increase operator safety.
- Innovative packaging such as right-size weighing, single-use powder transfer bags, and specialty solutions for hygroscopic salts can simplify processes and streamline manufacturing.

Enhancing the Taste of Liquid Formulations
An unpleasant or bitter tasting oral liquid formulation will result in poor patient compliance, especially among pediatric patients. Enhancing the taste of these formulations requires consideration of many factors including sweetness potency, flavor, mouthfeel, and aftertaste, as well as ensuring safety and stability.
- Masking the bitterness of APIs and improving the sweetness profile of the formulation is a highly effective approach to increase acceptance of the final dosage form

Ensuring the Long-Term Stability of Liquid Folate
Folates are an essential B vitamin used to promote health and well-being. The stability of folate, including its synthetic form folic acid, however, is compromised by oxidation which presents a challenge for liquid formulations of the vitamin.
- Arcofolin® is a proprietary L-5-methyltetrahydrofolate that has long-term stability in solution. It is directly bioavailable in its active form, more rapidly absorbed, and doesn’t mask a B12 deficiency.
Related Product Resources
- Excipients for Your Liquid Application
Whether you are developing solutions, emulsions or suspensions – we provide high-quality pharmaceutical excipients for liquid formulations.
- Granulated Materials
Free-flowing and easy to handle, our granulated raw materials reduce caking and clumping for enhanced processability, improving both your manufacturing speed and operator safety.
- Injectables & Parenteral Formulations
Find high-quality, pure, and reliable raw material solutions to meet your parenteral formulation requirements.
- API Processing Chemicals
Find high-quality API processing chemicals to enhance API solubility. Our materials can help you with salt formation, co-crystal formation, polymorph screening, and nano-milling.
Web Tools
- Pharmaceutical Application Guide
Explore products and services for each step of your pharmaceutical manufacturing process
- Parenteral Process Guide
Find information on process design considerations at key steps of a parenteral process
- Risk Mitigation Tool
Get guidance through the challenges and quality requirements of your bio-manufacturing process
- Formulation Product Finder
Quickly sort our excipients and API portfolio by dosage form, application, and many other parameters

Overcoming increasingly complex obstacles in small molecule drug manufacturing requires a strategic approach to processing, formulation, regulatory compliance, raw material quality, and supplier selection.
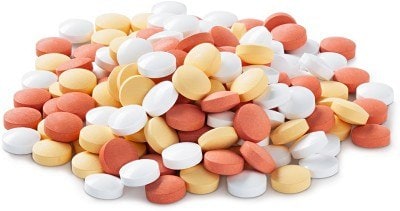
Solid dose challenges include API solubility and final formulation API stability, controlling total cost of manufacturing, and creating a robust, homogeneous tablet free of complications during packaging or storage.

Drug products must be free from bacteria and other microorganisms to ensure patient safety, requiring expert use of aseptic filtration for pharmaceutical products that cannot be terminally sterilize.

The final fill process is a critical aspect of drug manufacturing, demanding careful risk mitigation in order to ensure that safe therapeutic drug products are provided to patients.
To continue reading please sign in or create an account.
Don't Have An Account?