SMASH Packaging
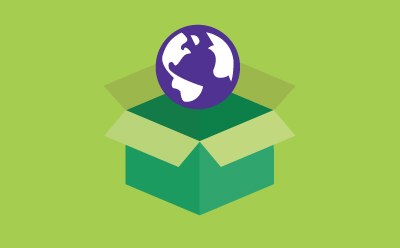
Our Approach
As part of our commitment to reduce our environmental impact, we have collaborated with internal and external stakeholders to establish a packaging sustainability framework to strategically drive significant sustainability improvements in our packaging by 2022.
We call it SMASH Packaging.
Our Actions and Results
We are implementing new sustainability standards and guidelines to develop and redesign our product packaging.
We identified three focus areas with the greatest opportunity for improvement that we call “pillars.” Within each pillar, we have defined four overarching goals to quantify, track, and increase our impact:
- Shrink: Reduce amount of packaging
- Secure: Achieve zero deforestation
- Switch: Improve plastic sustainability
- Save: Maximize recycling
We have established specific targets for 2022 for each of these goals. You can view our progress on these goals or download a copy of our 2021 Annual Update.
Our 2022 Goals and Targets
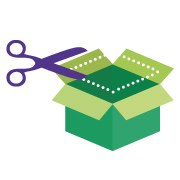
Shrink – Reduce Amount of Packaging
Our aim is to eliminate the use of packaging that is excessive in size or weight which unnecessarily consumes more resources, increases energy use and air emissions during transportation. Excess packaging is also undesirable for our customers since there are costs associated with the management and disposal of the packaging.
Our 2022 targets are:
- New product packaging aligned with our standards for weight and volume
- 20 key improvement projects for existing packaging
- 20% reduction of air space in distribution boxes
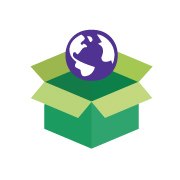
Secure – Achieve Zero Deforestation
Deforestation is a significant source of global warming and is a threat to biodiversity. Our aim is to ensure that the wood and fiber-based packaging materials that we use do not contribute to deforestation.
Our 2022 targets are:
- New product packaging aligned with our zero deforestation standards
- 90% of existing packaging aligned with our zero deforestation standards
- 100% of packaging from deforestation-risk countries certified sustainably sourced
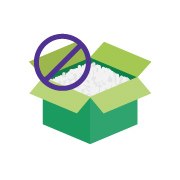
Switch – Improve Plastic Sustainability
Conventional plastic packaging has several sustainability issues associated with it. Our aim is to improve sustainability of plastic materials used in packaging applications, including increasing the use of materials with lower environmental impacts and reducing the use of plastics produced with chemicals of concern.
Our 2022 targets are:
- New product packaging aligned with our plastic sustainability standards
- 20 improvement projects to replace existing plastic packaging by more sustainable solutions
- 20% reduction of Expanded Polystyrene (EPS)
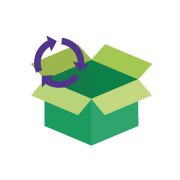
Save – Maximize Recycling
Our aim is to maximize recycling of our packaging materials by eliminating the use of packaging materials that are not compatible with recycling and by providing our customers with recycling guidance for all our packaging materials.
Our 2022 targets are:
- New product packaging aligned with our standards for recyclability
- 100% of fiber-based packaging not compatible with recycling, replaced
- 100% of products with packaging recycling/disposal guidance
To continue reading please sign in or create an account.
Don't Have An Account?