Closed Processing for Biomanufacturing
Closed Processing
The facility of the future will require transformation in how biologics are developed and manufactured. Closed processing mitigates contamination and safety risks, maximizes new and existing facility and asset utilization, while enabling sustainable multi-modal manufacturing. With closed processing costly cleanroom and environmental control measures are reduced without compromising product quality. Simplified space design, smaller cleanroom footprints, and increased operational flexibility allow for dramatic cost savings and future-readiness, today.

Close your process. Open your possibilities.
With closed processing, you can:
- Mitigate contamination and safety risks
- Reduce costly and environmentally demanding cleanroom control measures without compromising product quality
- Enable connected and continuous process manufacturing
- Maximize operational flexibility
- Enable sustainable multi-modal manufacturing
Download our white paper – "Perspectives on: The Adoption of Fully Closed Processing for Biopharmaceutical Manufacturing"
We conducted a global market survey on fully closed processing and gathered industry viewpoints on the topic. Our white paper provides key findings from the research, as well as insights and perspectives from industry experts on the shift towards closed processing and its effects on the facility of the future. Complete the form below to download our paper.
All fields with * are mandatory.
Value drivers & benefits of closed bioprocessing
![]() |
47% reduction in contamination risk |
![]() |
81% reduction in gowning costs |
![]() |
47% reduction in labor time due to reduced gowning, room cleaning, and equipment sanitization |
![]() |
Up to 53% reduction in environmental monitoring |
![]() |
Up to 65% reduction in energy consumption |
Related Podcast
Tune in & enter the world of Bioprocessing 4.0 with Merrilee Whitney, Chris Hwang and Kelvin Lee. In this podcast we discuss how to accelerate the production of biologics to a rapid pace.
Related Webinars
Uncover the benefits and challenges associated with closed processing and learn how innovations in closed single-use systems are driving greater manufacturing efficiency.
In this webinar, we present the design and performance testing of a single-use manufacturing-scale TFF system that can be operated in functionally or fully closed mode.
Learn about regulatory expectations when implementing single-use systems for final filtration and filling applications.
In this webinar, we discuss important elements of the revision to EU GMP Annex 1 and how single-use filtration systems can contribute to a holistic contamination control strategy.
External Articles
BioPharm International: Perceptions and Considerations for Adopting Closed Processing
Express Pharma: Is closed processing a reality?
Proof of Closure: Life Cycle of Closed Systems | Pharmaceutical Engineering (ispe.org)
Biosimilar Development: Transition To Closed Processing Systems For The Expansion Of Suspension Cells And Introduction Of Ballroom Format Cleanrooms For Cell Banking
Related Resources
Brochure: Process Development and Drug Manufacturing: Support Services
We provide comprehensive services for drug development and manufacturing, including technical and regulatory expertise and process development support.
BioContinuum™ Platform: Your enabler of the biomanufacturing facility of the future!
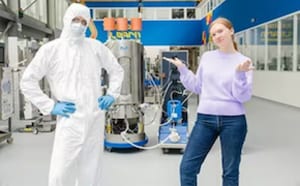
Pour continuer à lire, veuillez vous connecter à votre compte ou en créer un.
Vous n'avez pas de compte ?