制成品灌装策略

一次性技术无需清洁和验证步骤,节约了生产时间和成本。但在享受这些益处的同时,还需考虑新的因素,包括塑料组件化学相容性、从最终用户到供应商的关键验证策略调整。
优化无菌采样方法
更严格的验证要求以及质量源于设计(QbD)理念和工艺分析技术(PAT)更多地运用,要求对抽样过程进行更严格的审查。由于制造系统中的开放端口存在污染风险,并且操作人员可能出错,传统的采样方法无法满足监管机构要求。
运用优化的采样工艺可降低风险,提高生产率。为此,可采用一种有效的无菌采样系统,借助良好的采样操作规范监控过滤器有效性、评估工艺和产品质量,减少污染概率。
评估一次性组件的化学相容性
一次性设备通常采用聚合材料制成。根据化学成分,工艺流体可能会与这些聚合物发生不良相互作用。此时的难点在于寻找到与生产商原料和过程流体都相容的结构材料。此外,通常很难找到证明化学相容性所需步骤的详细指南。法规和指南文件的内容涵盖了各种各样的产品和工艺流程,却未提供证明相容性的具体方法或程序。
药品生产中一次性设备和材料的正确选择和鉴定应包括接触产品组件的化学相容性全面评估。因此,与具备以下特征的供应商合作很重要:
- 理解生产商工艺流程,对一次性材料有深入的了解
- 可协助评估工艺风险,就如何适当降低风险提出建议
凭借妥善的装配设计满足制成品灌装工艺严格要求
在制成品灌装过程中,一次性技术应用正在稳步增加。一次性技术需要满足制成品灌装工艺步骤的严格要求,即流体路径无菌性、完整性、操作安全性并且适合一次性组件用途。全新一次性制成品灌装解决方案可以通过适当的组装设计有效地满足上述要求,集成至灌装设备中。风险评估和合规性是无菌过滤工艺设计的关键考虑因素之一,因此有必要评估正确验证支持所需的支持文档。
提高生产率并管理风险
药品生产商承担着高效、有效推进管线资产的压力,同时还要将产品损失、产品污染、无菌和患者安全性相关的风险降至最低。一次性制成品灌装组件可以提高灌装生产线的生产效率,根据各种药品和填充量灵活调整,同时降低污染风险。但一次性制成品灌装组件可能面临管理实施和法规风险的挑战,需要进行严格的工艺验证确保符合法规指南。为确保通过此类验证可采取的步骤为:
- 针对装配制造和灌装工艺进行系统、全面地评估
- 准确解读法规要求
- 采取分步方法,识别并降低与工艺流程组件相关的风险
工作流程

传统药物的配制和生产
克服小分子药物生产日益复杂的阻力需要在工艺、制剂、合规性、原料质量和供应商遴选等环节采取策略性方法

液体制剂策略
由于无菌液体产品用药常需注入体内,因此必须尽可能降低相关风险,可行的措施包括遴选适当的API纯化工艺、确定适宜的辅料、明确适当的工艺验证方法并妥善选择配套过滤器。
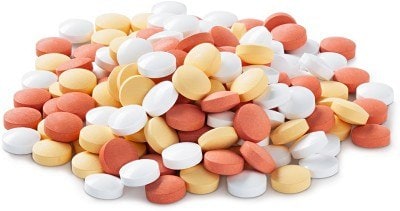
固体制剂策略
固体制剂面临的挑战包括,API溶解性和最终制剂API稳定性、控制生产总成本并生产稳定均匀的片剂,确保包装或存储过程不会出现任何适应症。

无菌过滤策略
为确保患者安全,必须去除药品中的细菌及其他微生物污染,为此需要针对无法最终灭菌的药品采取专业无菌过滤工艺。
支持技术内容
若要繼續閱讀,請登入或建立帳戶。
還沒有帳戶?