MRT - Mono-Boc-Protection of Diamines
Benefit from MRT & Flow Chemistry: Green production of a highly pure product with 100% yield from precise control over reaction temperature.
Mono-Boc-protected diamines are versatile building blocks for chemical synthesis. Their production is a lot more challenging than the simple reaction scheme might imply, because the Boc-anhydride reagent cannot differentiate between the two identical amino moieties in the substrate. The result is a crude mixture of unprotected, monoprotected and di-protected diamine (Scheme 1).
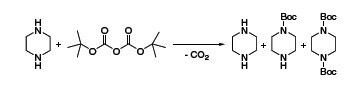
Scheme 1.Retinol synthesis
The preparation of mono-boc-protected piperazine is a good example of how one can perform a rapid process development for such a synthesis project with microreactor technology.
In a first series of 7 experiments, the reaction was tested with a couple of solvents at different temperatures. Apolar solvents like dichloromethane or toluene lead to the formation of solid particles and the blockage of the microreactor even at elevated temperatures. Methanol was able to keep all reagents and products in solution at room temperature, and was used for all further experiments.
In a second set of 6 experiments, the molar ratio between the bocanhydride and the diamine was optimized. This task was accomplished a lot more easily with flow chemistry than with batch experiments. Batch reactions require individual set-up for every data point where as with flow chemistry one simply keeps the flow rate for one reagent stream constant. The flow rate in the other channel is changed stepwise and a product sample is taken after each change. Analysis of the data of this case showed that a maximum yield for the desired mono-protected piperazine was achieved with the addition of 0.8 equivalents of Boc-anhydride. Any less or more of the reagent then either the untouched piperazine or the di-protected product becomes predominant. The maximum yield of the reaction under optimal conditions in the microreactor is 45%. This does not seem very impressive however, it is significantly better than results achieved with batch reactors.
Industrial production requires further considerations for maximizing the product output over time. In flow chemistry, the output over time depends on concentration and flow rate. A series of three experiments allowed us to determine that 1.3 M of piperazine in methanol was the optimal concentration to avoid product precipitation blocking the system. Subsequent experiment series determined the optimal concentration of Boc-anhydride in the second channel (1.04 M, 0.8 eq), and the optimal flow rate (4mL/min), where the temperature was kept constant at 30 °C and the fixed residence time of 75 mL was used.
The best parameters found for the production of 600 g mono-Bocprotected piperazine were achieved in 8 hours with 20 measurements. The procedure can typically be optimized for similar substrates in less than a day.
To continue reading please sign in or create an account.
Don't Have An Account?