Materials for High and Low Refractive Index Coatings
Introduction
Refractive index (RI or n) is of critical importance for photonics applications such as optical waveguides and ophthalmic devices. Based on their unique refractive index characteristics and good optical clarity, polymeric materials are also used as anti-reflective coatings for solar cells, displays and contact lenses.1,2 With the need for mechanical strength, environmental stability, and ease of processing, polymeric-based materials have the potential to be excellent alternatives to traditional inorganic optical films.3 Other advantages over their inorganic counterparts include light weight, insensitivity to vibrational stress, and low cost.
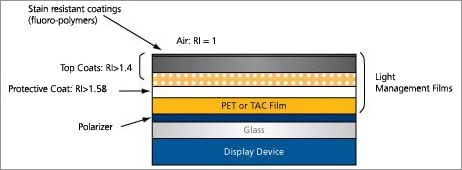
Figure 1.Schematic of a display (e.g. LCD) with protective and RI-control polymer overlayer films image
Anti-reflection coatings for LCD displays are one example of an application that uses polymeric RI-control technology (Figure 1). Films of PET (polyethylene terephthalate) or TAC (triacetyl cellulose) are typically applied to protect outer layers of modern multi-layer LCD stacks. PET and TAC are inexpensive strong polymers with n ~ 1.7 much larger than for air (n = 1). A large fraction of light beam incident on an abrupt interface with ?n ~ 0.7 would bounce off (reflect) from the interface. For an LCD, this would result in a significant fraction of ambient light reflected from the display surface, causing glare and wash-out of displayed images. To solve this problem, a light management film stack with gradually varying RI can be applied to the LCD surface. The stack consists of multiple layers with gradually diminishing RI from high adjacent to the PET/TAC surface to low facing air. By matching the refractive index of the display surface to that of air, surface reflection is reduced, leading to higher effective image contrast and reduced washout by ambient reflections.
Zirconium and Hafnium Acrylate Monomers
RI engineering of light management stacks depends on availability of additives to adjust (raise or lower) RI of polymer films. Possible RI-raising additives include metal-oxide nanoparticles and monomers/polymers containing atoms with high (compared to carbon) atomic numbers. Zirconium and hafnium based acrylate monomers newly available in our catalog (Table 1) are particularly well suited for controlling RI of acrylate films, for example urethane acrylates commonly used to formulate protecting films of LCD displays. Cured acrylate films incorporating these products are UV-stable and combine:
- Excellent optical clarity (>95%)
- Good hardness and scratch resistance (>2H Pencil Hardness)
- >Tuning of RI by choosing loading of functional monomer (Figure 2)
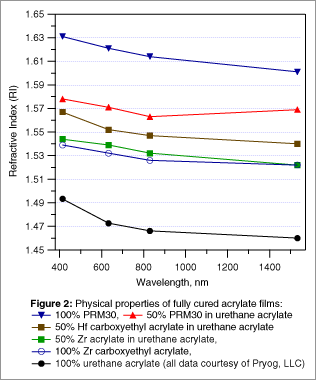
Figure 2.Physical properties of fully cured acrylate films
High and Low RI Polymers
In addition to the polyfunctional zirconium and hafnium acrylates, we offer a range of high RI polymers based on aromatic and brominated aromatic monomers (Table 2), as well as low RI materials based on fluorinated monomers (Table 3). The associated monomers are also available and can be used to synthesize polymers whose refractive index can be tailored. Also listed are UV/thermal crosslinkable polymers for patterning or heterolayered device fabrication. The tables list products sorted in order of refractive index and can be used as material selection tools for your photonics research.
Para seguir leyendo, inicie sesión o cree una cuenta.
¿No tiene una cuenta?