3D Printing Graphene Ink: Creating Electronic and Biomedical Structures and Devices
Adam E. Jakus, Ph.D.1,3, Ramille N. Shah, Ph.D.1,2,3
1Materials Science and Engineering, McCormick School of Engineering, Northwestern University, Evanston, IL 60208 USA, 2Comprehensive Transplant Center and Department of Surgery, Feinberg School of Medicine, Northwestern University, Chicago, IL 60611 USA, 3Simpson-Querrey Institute for BioNanotechnology in Medicine, Northwestern University, Chicago, IL 60611 USA
Material Matters, 2016, 11.2
Introduction
Since its discovery little more than a decade ago,1 the two-dimensional (2D) allotrope of carbon—graphene—has been the subject of intense multidisciplinary research efforts. These efforts have not only revealed the exceptional electrical,2 mechanical,3 thermal,4 and biological5,6 properties of graphene, but have also lead to the discovery of an entire class of 2D materials with unique and potentially highly advantageous properties.7 As the knowledge and understanding of graphene and its properties has grown, so too has the interest in elevating this material from a scientific curiosity to a material that can be widely and readily applied to a broad range of applications and devices.
The growing interest in graphene has led to commercial efforts to produce graphene and its derivatives at scale. As a result, graphene is now available in a variety of forms, including unmodified and modified powders, films, liquid suspensions, and more. More recently, the development and availability of new, easy-to-utilize graphene-based 2D and three-dimensional (3D) printing inks8–10 (Prod. Nos. 798983, 793663, 796115, and 808156) provide researchers with the necessary tools to develop and engineer graphene-based devices and applications in many areas such as flexible electronics and sensors,9,10 bioelectronics, and nerve, muscle, and bone tissue engineering constructs and devices.8
2D vs. 3D Graphene Printing Inks
It is important to distinguish between 2D inks intended for the fabrication of planar devices and 3D inks intended for the fabrication of volumetric constructs and devices (Figure 1).8,11,12 The rapidly emerging worldwide interest in 3D printing from consumers, researchers, and those interested in the industrial production of end-use parts has generally outpaced an adequate understanding of the underlying technologies, their uses, restrictions, and requirements, particularly 3D printing materials. This has frequently resulted in unintentional but false equivocation of established 2D printing technologies with newer 3D printing technologies and associated materials and their uses.
2D graphene inks generally make use of well-established inkjet10 and gravure-related9 printing hardware and processes. The 2D processes utilize 2D inks with similar requirements as those used for inkjet printing, including low viscosity (Figure 1). The need for low viscosity limits the maximum graphene content within the ink, but enables very rapid, highly precise deposition of material onto flat substrates. The resulting small or large area 2D graphene structures retain mechanical flexibility, high electrical conductivity, and thermal and chemical stability after deposition,9,10 making these materials exceptionally useful for a variety of current and future electronic and energy applications.

Figure 1.Characteristics comparison of 2D and 3D graphene inks, their deposition processes, and printed material characteristics.
Graphene has also demonstrated substantial promise for 3D materials fabrication.8 For example, an extensive variety of graphene-containing composite foams,13 hydrogels,14 and thermoplastics15 are already in use. 3D printing graphene inks are a new class of graphene materials that can be utilized to rapidly create user-defined 3D graphene structures.8 Unlike 2D graphene inks, which do not need to be mechanically self-supporting upon deposition onto a substrate, 3D inks must satisfy a much broader set of requirements,11 such as retaining significant material functionality as well as having the ability to be printable into volumetric structures comprised of one to many thousands of layers. We have developed 3D printing inks that are printed via room-temperature extrusion from a mechanically or pneumatically driven syringe (Figure 1) in much the same way an individual uses a standard syringe to extrude material from a needle or nozzle by hand. The 3D inks and associated room-temperature extrusion 3D printing process are distinct from the widely used fuseddeposition modeling (FDM) 3D printing approaches, which utilize thermoplastic filaments extruded at elevated temperatures.
3D printing graphene inks8 and related materials employ an evaporation driven solidification mechanism, whereby an ink is formulated by dissolving a polymer in a fast-evaporating solvent such as chloroform or dichloromethane. The ink is extruded at ambient or near ambient temperatures and rapidly solidifies as the solvent evaporates and the polymer comes out of solution. These 3D inks are user friendly, easily printable, print very rapidly, and exhibit highly advantageous functional materials properties.
3D Printing Graphene Ink Characteristics
3D printing graphene ink8 (Prod. No. 808156) is a moderate viscosity (25–35 Pa.s) graphene suspension comprised of graphene, dissolved elastomeric polymer binder, and a mixture of solvents that can be 3D printed (or used with any standard syringe) from a nozzle (50–2,000 μM in diameter; Figure 2A) under ambient conditions to rapidly create 3D graphene-based constructs that can be handled immediately (no drying time required; Figure 2B). The resulting 3D printed material is comprised of 60 vol.% graphene and 40 vol.% elastomeric polymer. Due to the rapid solidification of the 3D printing graphene ink, it must not be exposed to an open environment for an extended period of time when not in use. It may be possible to recover dried inks by adding a small volume of dichloromethane (Prod. Nos. 270563, 676853, 320269, and more) followed by mechanical stirring or shaking to homogenize. However, inks that are reconstituted in this way tend to suffer from more nozzle clogging events than the unreconstituted native inks. The solvent contents of the 3D inks also require that they not be exposed to materials that are soluble in dichloromethane, including polystyrene and low density polyethylene, prior to washing (more on washing in the following sections).
3D-printed Graphene Objects
A syringe-based 3D printer is not required to use the 3D printing graphene ink, although it is desirable for precision X, Y, Z spatially controlled deposition of the material. In place of a 3D printing platform, a standard hand or mechanically driven syringe may be used to extrude the 3D printing graphene inks and produce solid structures. Due to the elongated morphology of the comprising graphene flakes and shear forces from nozzle extrusion, the 3D printed graphene adopts a micro-texture defined by the lengths of the individual graphene particles aligned with, and stacked perpendicular to the fiber direction (Figure 2D).8 Fabrication of multi-layer graphene objects is done through deposition of sequential materials in a pre-defined pattern and predefined object geometry (Figure 2C). The software associated with defining internal patterns and overall object geometry varies greatly and is typically specific to individual 3D printing platforms.

Figure 2.A) Photograph of graphene fibers extruded from nozzles with indicated diameters. Typically, the rapid drying of the 3D printing graphene ink upon deposition results in a 10% diameter reduction (i.e., Ink extruded from 100 μM tip results in ~90 μM fiber). B) Photograph of a variety of few- and many-layer graphene architectures 3D-printed from the 3D printing graphene ink using a range of nozzle diameters. C) SEM of 0–90° alternating and 0–120–240° alternating graphene structures produced from 3D printing graphene inks and extruded from 100 and 150 μM nozzles, respectively. D) Scanning electron micrograph (SEM) of surface and interior 3D-printed graphene fiber of 100 μM diameter. Modified from Reference 8.
Versatility and Handling
A 3D-printed graphene object can be physically handled immediately after production and is surprisingly robust despite the high graphene content. Residual solvents can be removed by washing objects in 70% ethanol.8 Few-layer objects, such as sheets, can be rolled, folded, and cut in a similar manner to standard paper (Figure 3A). Even thick objects can be cut or “punched” to yield many samples of defined sizes from a single 3D-printed object (Figure 3B). Finally, the nature of the 3D printing graphene inks enables independently 3D-printed graphene objects to be fused together to create larger and/or much more complex objects than could be 3D-printed directly (Figure 3C). This is achieved through conservative application of small volumes of graphene inks at contact surfaces of one or both of the parts to be joined. The freshly deposited ink locally dissolves the polymer matrix in the 3D-printed graphene and rapidly evaporates, bringing the just-dissolved polymer out of solution and creating a mechanically and electrically seamless interface between the joined objects.8

Figure 3.A) Graphene structures from 3D-printed graphene inks are flexible, and in the case of sheets (8 cm diameter), can be easily rolled, folded, cut, etc. B) Smaller graphene objects can also be directly cut or punched from larger 3D-printed graphene objects. This photo illustrates circular graphene samples punched from the 25-layer graphene square shown in Figure 2. C) Photograph of anatomically correct, scaled human skull, mandible, and upper spine produced by fusing five independently 3D-printed graphene parts together by lightly applying 3D printing graphene inks at points of contact.
Mechanical, Thermal, and Electrical Properties
3D-printed graphene objects derived from 3D printing graphene inks are mechanically plastic in nature (Figure 4A,4B),8 can undergo substantial strain (>80%) prior to failure, and exhibit yield and ultimate tensile strengths of less than 1 MPa. Thus, 3D-printed graphene objects are relatively soft in nature and can be shaped and modified after 3D printing to suit individual requirements. Although graphene itself is compatible with high temperatures,4 the elastomeric matrix (responsible for the highly versatile mechanical properties), comprising 40% of the solids volume of the material, is not. The polymer will decompose at temperatures at or above 150 °C, which causes the material to become mechanically brittle (Figure 4B),8 even though the 3D-printed architecture is maintained.
Due to the high graphene content, objects created from 3D printing graphene inks are electrically conductive, exhibiting as-printed conductivities in excess of 650 S/m, which can be improved to >870 S/m if the material is thermally annealed in air at 50 °C for approximately 30 minutes (Figure 4C).8 This is the highest recorded conductivity for a 3D-printed material that is not a metal or alloy. The nature of the ink and 3D printing process also ensures that printed layer boundaries do not act as electrical defects, which would otherwise inhibit conductivity across small and large objects.

Figure 4.A) Despite the exceptionally high graphene content, 3D-printed graphene objects are relatively soft and can withstand upwards of 80% tensile strain. B) Under compression, 3D-printed graphene objects plastically deform if not previously heated to temperatures ≥150 °C. C) Photograph illustrating electrical conductivity of a 3D-printed graphene object (triple helix shown in Figure 2). Adapted from Reference 8.
Biological Properties
Bioactivity and the potential of biocompatibility are the most exceptional aspects of 3D-printed graphene from 3D printing graphene inks.8 Once washed to remove residual solvents, 3D-printed graphene contains only graphene flakes, and a biocompatible elastomeric polymer. In vitro studies using bone marrow derived adult human mesenchymal stem cells (hMSCs) and cultured in standard DMEM (Dulbecco’s Modified Eagle’s medium) growth medium with fetal bovine serum (no biochemical, mechanical, or electrical differentiation cues) illustrate that 3D-printed graphene not only supports stem cell viability (Figure 5A) and proliferation over the course of at least weeks, but that the stem cells begin differentiating into glial and neuron-like cells, as indicated by both gene expression and cell morphology (Figure 5B).8 This is remarkable, and the first time a material alone (without additional biological factors) has induced such strong neurogenic behavior in adult human stem cells. Preliminary in vivo experiments using a BULBc mouse subcutaneous model reveal that over the course of 7 and 30 days, native tissues rapidly integrate with and vascularize the implanted 3D-printed graphene constructs (Figure 5C–F) with no significant immune response.8 Combined with its ability to be 3D-printed into nearly any form, its ability to be mechanically manipulated, its electrical conductivity, and its bioactivity, 3D-printed graphene is an excellent addition to the 3D printing biomaterials palette,11 with many fundamental and translational applications on the horizon.
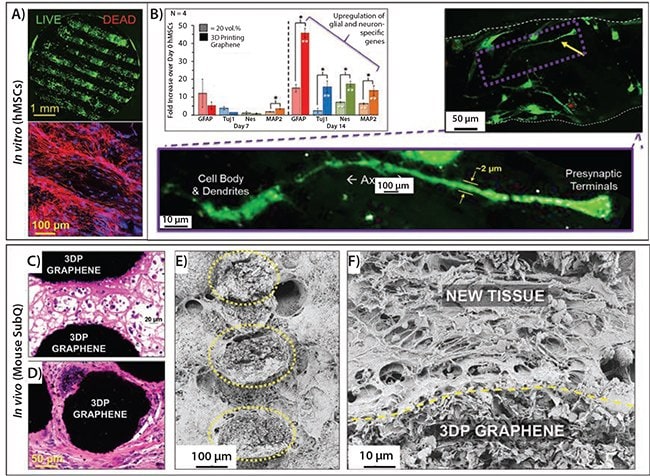
Figure 5.A) Top: Confocal microscopy reconstruction, top-down view of live (green) and dead (red) human mesenchymal stem cells on 3D-printed graphene 21 days after initial cell seeding; Bottom: confocal microscopy reconstruction showing cytoskeletal extensions (red) and cell nuclei (blue). B) Glial and neurogenic-relevant gene expression of hMSCs on 3D-printed graphene and lower content graphene material, 7 and 14 days after initial cell seeding and cultured in simple DMEM + FBS medium. Corresponding images are live/dead confocal reconstructions of hMSC derived neuronlike cells on 3D-printed graphene 14 days after initial seeding. Modified from Reference 8. C) H&E histological micrograph of 3D-printed graphene scaffold explanted 7, and D) 30 days after subcutaneous implantation into the backs of female BULBc mice. Black is the cross-section of individual 3D-printed graphene struts comprising the scaffold, pink is new cellular and extracellular tissue, and purple/ blue are cell nuclei. E) SEM of 3D-printed graphene scaffold and integrated tissue 7 days after subcutaneous implantation into mice. Cross-section of comprising graphene structures, outlined by yellow dotted lines. F) SEM micrograph of day 30 explanted in vivo 3D-printed graphene sample showing tight interface between 3D-printed graphene material and new, integrated tissue.
Conclusions and Future Prospects
Recent developments in 2D and 3D printable graphene-based materials are beginning to bring the story of graphene full circle; from the discovery of graphene little more than decade ago, to the extensive fundamental research into its properties and their underlying mechanisms, to large-scale synthesis, to the development of ready-to-use graphene materials for device research and engineering. Based on these rapid developments and continued interest, it is safe to say that graphene materials are successfully making the transition from scientific curiosity to an indispensable tool, forming the foundation for the development of a broad array of new, advanced electronic, bioelectronics, and biomedical technologies.
Acknowledgments
The authors acknowledge the support and the use of the following facilities: Northwestern University Cell Imaging Facility supported by NCI CCSG P30 CA060553 awarded to the Robert H. Lurie Comprehensive Cancer Center; EPIC facility (NUANCE Center_Northwestern University) supported by NSF DMR-1121262 and EEC-0118025|003; Northwestern University Mouse Histology and Phenotyping Laboratory and Cancer Center supported by NCI CA060553; and the Equipment Core Facilities at the Simpson Querrey Institute for BioNanotechnology at Northwestern University developed by support from The U.S. Army Research Office, the U.S. Army Medical Research and Material Command, and Northwestern University. This research was also supported by Northwestern University’s International Institute for Nanotechnology (NU# SP0030341), Northwestern University’s McCormick Research Catalyst Award and the Office of Naval Research MURI Program (N00014-11-1-0690).
References
계속 읽으시려면 로그인하거나 계정을 생성하세요.
계정이 없으십니까?