Quality & Regulatory Trends
The life sciences industry operates in one of the world’s most regulated environments. Today, we are facing increasing regulatory requirements and complexity.
As a global leader in the Life Science industry, we are on top of current trends and future quality and regulatory opportunities as well as challenges. We support our customers to navigate and comply with a highly complex set of global, regional, country, and industry-specific directives and regulations.
Regulatory Trends in the Pharmaceutical Industry
Pharma Ingredients (Active Pharmaceutical Ingredients & Excipients)
New Chinese Regulation for Excipients and Active Pharmaceutical Ingredients (API)
With a population of 1.4 billion and an aging society, China is a highly attractive market for pharmaceutical companies. However, the outstanding market opportunities are accompanied by substantial challenges for companies who want to manufacture, import or sell drugs in China
The recent reforms have increased regulatory efficiency and transparency and have to some extent resulted in a better alignment with international standards. In August 2019, the China Drug Administration Law has been revised, with changes that came into effect on December 1st, 2019. This law aims at enhancing drug safety and improving public health. It includes most of the previous reform outcomes such as the China Marketing Authorization Holder system but also the mandatory registration and the co-review regulation relevant for APIs, excipients and packaging alike.
According to the current regulation NMPA Number 146 (Former CFDA Number 146), API and excipients manufacturers need to submit a registration dossier to NMPA (National Medical Products Administration, formerly Chinese Food and Drug Administration, CFDA) to obtain a registration number. The registration numbers are officially published on the Center of Drug Evaluation (CDE) homepage: http://www.cde.org.cn/yfb.do?method=main. Then, the drug manufacturer needs to have a Letter of Access (LoA) issued by the API/excipient manufacturer to refer to the registration number for their drug application. In addition, the registration dossier of the API/excipient will be co-reviewed within the drug application.
Related Whitepaper
Chinese Excipients Regulation –
a Globally Unique Challenge (PDF)
Related Webinar
We are willing to support our customers for their drug applications including our excipients and APIs. Our registration numbers are available on the CDE website.
Download our current registration dossier list including co-review status (PDF)
For more information about registration dossiers or for your request for LoA, please contact your local representative.
Elemental Impurities.
Elemental Impurities are mostly metal residues. Metals in medicinal products may also be present as impurities. Contamination may arise from metals deliberately added as catalysts or reagents, natural source materials (e.g. in minerals or herbals), or processing equipment (like vessels, pipes or metal connections to tubes or hoses) may be further causes for metal residues. They may exert toxicological effects and therefore they should be excluded or limited.
In Europe, the ICH Q3D guideline is effective since June 2016 for new Drug Products (also new DP with existing Active substances – that means new generic products) and since Dec 2017 for existing DP.
Our Life Science business has set up a project to proactively generate data on elemental impurities to support our customers. EII (Elemental Impurity Information) Dossier is also part of our new Emprove® "Operational Excellence Dossier".
NSF/IPEC/ANSI 363– 2014 Good Manufacturing Practices (GMP) for Pharmaceutical Excipients.
The new voluntary standard, “NSF/IPEC/ANSI 363 – 2014 Good Manufacturing Practices (GMP) for Pharmaceutical Excipients” was published in December 2014 after a lengthy publication timeline. This standard is a joint publication by NSF (which develops standards and certification programs), IPEC (International Pharmaceutical Excipients Council), and ANSI (America National Standards Institute). This Standard is intended to define Good Manufacturing Practices (GMP) for excipient manufacturing and distribution for use in drug products. It sets minimum requirements for GMP applicable to all commercially available excipients.
Our manufacturing site in Darmstadt holds a joint EXCiPACT™/ NSF/IPEC/ANSI 363-2014 US National Standard certification since April 2016. This extended certification of the pharmaceutical excipients of the Emprove® brand shall specifically address the needs of the US market. NSF/ANSI Standards have a high reputation in the US and support sales into that market.
Pharma Materials (SUS, Filter, CCM)
USP <665>: Polymeric Components and Systems Used in the Manufacturing of Pharmaceutical and Biopharmaceutical Drug Products.
USP <665> addresses the qualification of polymeric components used in the manufacture of both pharmaceutical and biopharmaceutical APIs and drug products. It is applicable to filter products, chromatography media, single-use systems and any other components that are in fluid contact in manufacturing process.
The standard is applicable to all the Bioprocess products that have plastic components in liquid contact. The level of testing required is determined by performing a risk assessment and aligning to the appropriate risk level as outlined above. Extractables testing per a protocol described in this standard has to be performed for high risk levels.
The standard is still a draft and our Life Science business actively contributes to the commenting process.
Cell & Gene Therapies
Our Life Science business is actively working in the innovative discipline of Gene Editing and Novel Modalities to address our customers’ unmet needs by developing various solutions along the therapy development and manufacturing process.
The Cell Therapy group is working on developing modular, single-use, closed and automated systems for manufacturing cell therapies. Life Science also offer kits for gene editing useful in creating gene modifications. Our Life Science site in Carlsbad, California, USA, manufactures viral vectors and is a key contract manufacturing service for the industry. There are groups within Gene Editing and Novel Modalities working on optimizing the vector production process to improve yields. Our company proactively put in place several programs to develop solutions to address this novel market.
Regulatory Trends in the Food Industry
Food Defense Plan (FSMA)
The U.S. Food and Drug Administration (FDA) recently finalized the focused mitigation strategies to protect food against intentional adulteration (Food Defense) rule under the Food Safety Modernization Act (FSMA).
This rule addresses mitigation strategies to protect food against intentional adulteration and is aimed at preventing acts intended to cause wide-scale harm to public health, including acts of individual sabotage, terrorism and economically motivated adulteration. Together with hazard analysis and risk-based preventive controls for human food (PCHF), a rule that is intended to prevent unintentional adulteration, FSMA now obliges the food industry to a comprehensive assessment of potential adulteration. The rule requires domestic and foreign food facilities that are required to register under the Federal Food, Drug, and Cosmetic Act to create a food defense plan by July 26th, 2019.
Creation of a food defense plan is an approach comparable to HACCP (Hazard Analysis and Critical Control Points). This written plan must identify vulnerabilities and actionable process steps, mitigation strategies, and procedures for food defense monitoring, corrective actions and verification. A reanalysis is required every three years or when certain criteria are met, including mitigation strategies that are determined to be improperly implemented. The food defense plan should include mitigation strategies for both external threats to food safety as well as internal threats. Facilities therefore have to ensure that personnel assigned to the vulnerable areas receive appropriate training and maintain records for food defense monitoring, corrective actions, and verification activities. To support all required activities, the FDA offers various material on its FDA website.
Our Life Science business has set up a project for sites which are manufacturing food ingredients to develop a written food defense plan, to identify any significant vulnerabilities by an HACCP-type approach, and to implement mitigation strategies.
EU Food Contact Materials Regulation
There are several filter products that are also marketed within the food industry in Europe. When used in the manufacturing of food and beverages, these materials must comply with the European requirements for food contact materials.
A so-called "Declaration of Compliance" (DoC) for food contact material to demonstrate compliance to the provisions of Community legislation on plastic materials and objects in contact with foodstuffs (EU 10/2011) is available for our customers.
DoCs are available for selected products out of following product families:
- Bevigard™ (Bevigard™ P, Bevigard™ L, Bevigard™ M)
- Brewpore®
- Clarigard®
- Durapore®
- Lifegard™
- Milligard®
- Polygard®
- Polysep™
- Vitipore® II, Vititpore® II Plus
Regulatory Trends for Medical Devices/In Vitro Diagnostics
New EU Medical Devices and In Vitro Diagnostics Regulations, 2017
The new EU Medical Devices and In Vitro Diagnostics Regulations from 2017 are the biggest change in European regulations related to medical devices and in vitro diagnostics (IVDs) since the introduction of the current EU CE marking directives.
This has huge implications to the medical device industry in Europe, impacting all “economic operators” (i.e., manufacturers, importing or distributing devices into Europe, authorized representatives, notified bodies and competent authorities). Critical suppliers to medical device and IVD manufacturers will also feel the impact of the new regulations. The two new regulations were published in May 2017 with a three-year transition period for the Medical Device Regulation (MDR) and a five-year transition for the In Vitro Diagnostic Regulation (IVDR). The longer transition time for the IVDR, is due to the major change in classification from the old IVDD to the new IVDR and the subsequent impact this will have on IVD manufacturers.
The new regulations introduce a number of new requirements and changes. Some of the major changes include:
- Changes in the classification of IVDs which will lead to a greater number of IVDs requiring notified body conformity assessments
- New requirements for performance evaluation for IVDs including performance evaluation reports
- Introduction of a person responsible for conformity of the device before it is released
- Identification and traceability - introduction of Unique Device Identification Mandated (UDI)
- Strengthening of the position of Notified Bodies in relation to manufacturers including introduction of unannounced inspections
Our Life Science business has implemented a global project based around a core multi-functional global team providing expert project management, strategy, procedures/templates and guidance/training to local site teams and sub-teams to implement site specific project plans to meet the deadlines for the new regulations.
ISO 13485:2016
After more than ten years, the update to the global standard for medical device quality management systems (QMS) has been adopted. ISO 13485:2016 replaces previous version from 2003.
Up to March 2019, ISO 13485:2003 and ISO 13485:2016 will coexist, allowing manufacturers, accreditation/certification bodies and regulators time to transition to the new standard. The European harmonized version of the ISO 13485 standard is used to demonstrate QMS conformity for the CE marking of Medical Devices and IVDs under the current European Directives and new regulations. The new 2016 standard will also be used as the basis for the inspections under MDSAP (Medical Device Single Audit Program).
The changes between the 2003 and 2016 version include:
- Incorporation of risk-based approaches beyond product realization
- Risk is considered in the context of the safety and performance of the medical device and in meeting regulatory requirements
- Increased linkage with regulatory requirements, particularly for regulatory documentation
- Application to organizations throughout the lifecycle and supply chain for medical devices
- Harmonization of the requirements for software validation for different software applications (QMS software, process control software, software for monitoring and measurement) in different clauses of the standard
- Emphasis on appropriate infrastructure, particularly for production of sterile medical devices, and addition of requirements for validation of sterile barrier properties
- Additional requirements in design and development on consideration of usability, use of standards, verification and validation planning, design transfer and design records
- Emphasis on complaint handling and reporting to regulatory authorities in accordance with regulatory requirements, and consideration of post-market surveillance
- Planning and documenting corrective action and preventive action, and implementing corrective action without undue delay
Each of our ISO 13485:2003 certified sites are working on a gap analysis in partnership with their certification bodies to determine their individual plans for transition to the new 2016 version.
Industry Associations
We have a network of more than 90 Subject Matter Experts in 35 countries. This team is responsible for a structured ongoing monitoring of regulations with timely analysis and communications to our stakeholders. The Subject Matter Experts actively contribute in more than 80 industry associations and standard setting organizations

International Pharmaceutical Excipients Council. Serves the interests of producers, distributors and users of excipients. The expert organization for quality of excipients.

European Fine Chemicals Group. Advocacy activities related to fine chemicals, APIs and excipients. Represents chemical companies, national and European trade associations.
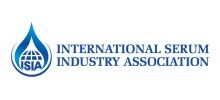
International Serum Industry Association. Primary focus on safety and safe use of serum and animal derived products through proper origin, traceability, truth in labeling and appropriate standardization and oversight. Network of companies handling serum and any type of animal material. Relationship to various veterinary authorities around the world, in particular to USDA.

Rx-360. An International Pharmaceutical Supply Chain Consortium to protect patient safety by sharing information and developing processes related to the integrity of the healthcare supply chain and the quality of materials within the supply chain.

Parenteral Drug Association. The leading global facilitator of science, technology and regulatory information. PDA technical reports are considered best practices and are often cited in regulatory guidelines.

Active Pharmaceutical Ingredients Committee. Focus is on worldwide Quality, Good Manufacturing Practice (GMP) and Regulatory matters relating to APIs and Intermediates. APIC is a high-profile industry association with an excellent, worldwide reputation.

Bio-Process Systems Alliance. Trade association dedicated on single-use manufacturing technologies used in the production of biopharmaceuticals and vaccines. Key association for the single-use systems technical and regulatory standard development.

BioPhorum Operations Group. Leaders of the biopharmaceutical industry focusing on the key operational challenges, improving competitiveness and reducing patient risk. Key industry association due to their influence from members which include most of big Biopharma Companies.

The European Chemical Industry Council or Cefic is the main European trade association for the chemical industry. It is a committed partner to EU policymakers, facilitating dialogue with industry and sharing broad-based expertise. The 670 members and affiliates form one of the most active networks of the business community, complemented by partnerships with industry associations representing various sectors in the value chain.

The United Nations (UN) is an intergovernmental organization tasked to promote international co-operation and to create and maintain international order. UN GHS, the Globally Harmonized System of Classification and Labelling of Chemicals, is an internationally agreed-upon standard managed by the United Nations that was set up to replace the assortment of hazardous material classification and labelling schemes previously used around the world.
To continue reading please sign in or create an account.
Don't Have An Account?