Gene Therapy Formulation and Final Fill

Formulating a gene therapy demands a high level of application and regulatory expertise. Viral vectors are subject to variations in process and in therapy dosages ruling out a one-size-fits-all approach. To minimize risk, gene therapies must be formulated to meet unique regulatory requirements, and deliver reproducible product quality, safety, yield, titer, and purity.
Throughout the formulation process, manufacturers must leverage application expertise, state-of-the-art production facilities, and regulatory knowledge that can be costly and time-consuming to develop in-house. Selecting a strong and experienced partner is a decision of critical importance, simplifying the complexity of supplier qualification and speeding up processes to reduce the total cost of ownership.
Related Product Resoruces
Webinar: Managing Implementation and Regulatory Risks: Single-use Technologies for Final Fill
Webinar: Final Filling Process Design Considerations, Part 1
Webinar: Final Filling Process Design Considerations, Part 2
Webinar: Final Filling Process Design Considerations, Part 3
Workflow
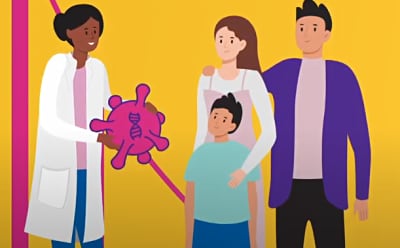

Viral Vector Upstream Processing
Making the right upstream process decisions not only impacts viral vector titer, but downstream processes, timelines, and regulatory acceptance

Viral Vector Downstream Processing
Efficient virus purification processes can improve yield, decrease time to patient, and lower manufacturing costs

Viral Vector Characterization and Biosafety Testing
Critical biosafety testing and characterization of viral vector products can help to fully analyze key quality attributes: identity, potency, safety, and stability

Gene Therapy Contract Development and Manufacturing
CDMO partnerships play a critical role in advancing clinical pipelines and achieving successful commercialization
To continue reading please sign in or create an account.
Don't Have An Account?